PE Pipe Extrusion Line
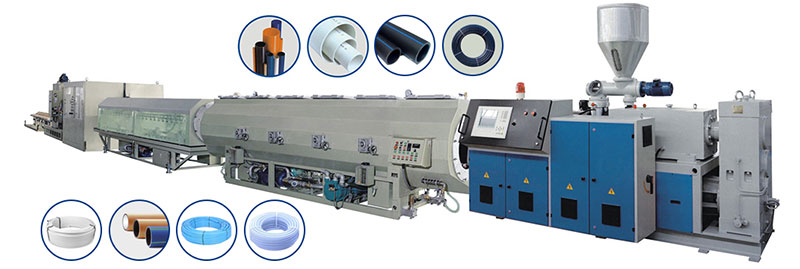
Pipe Diameter Range: Φ20 – Φ1200
1.Using high-efficiency extruder designed for special HDPE/PP pipes. The screw adopts a structure with a barrier and a mixing head. The barrel adopts a new type of slotting machine barrel. The plasticizing and mixing effects are good, and the extrusion volume is large and very stable.
2.The line adopts spiral die head that designed for HDPE/PP large-diameter thick-walled pipe. The die has the characteristics of low melt temperature, good mixing performance, low cavity pressure, and stable production.
3.The line uses a proprietary technology of sizing and cooling system, using water film lubrication and water ring cooling to meet the requirements of HDPE/PP materials, to ensure high-speed production of thick-walled pipes with stable diameter and roundness.
4.The line adopts specially designed vacuum calibration tank with multi-stage control vacuum degree to ensure the dimensional stability and roundness of HDPE and PP pipes. Extruder and Hauling-off machine adopt imported brand-name governor to control with good stability, high precision and high reliability.
5.The operation and time of the line is controlled by the PLC programmatically with good man-machine interface. All process parameters can be set and displayed through the touch screen. Special extruder for marking line can be assembled to produce national standards pipes with color marking.
We have high output single-screw extruder for PE extrusion line, adopting ultra-high torque United States Rexnord Group’s FALK-DHE2 series Reducer and specially designed barrel screw; the output can reach a level beyond the imagination in the realization of the ideal under the premise of plasticization (general equipment output limited to 3kg/kw , this equipment output can be greater than 4.5kg /kw).
Material + Color Masterbatch → Mixing → Vacuum Feeding → Raw Material Drying → Single Screw Extruder → Four Color Line Extruder → Basket or Spiral Mold → Sizing Sleeve → Spray Vacuum Forming Box → Spray Vacuum Forming Box → spray cooling water tank → spray cooling water tank → ribbon printing machine → crawler tractor → planetary cutting machine → pipe stacking machine → finished product testing packaging
Model | Diameter(mm) | Extruders | Max.Output(Kg/h) | Total Power(KW) |
GSPEG-110 | 20-63 | GS-SJ65/33 GS-SJ25/25 | 80-120 | 130 |
GSPEG-160 | 75-160 | GS-SJ65/33 GS-SJ25/25 | 120-220 | 130 |
GSPEG-250 | 110-250 | GS-SJ75/33 GS-SJ25/25 | 220-350 | 280 |
GSPEG-450 | 160-450 | GS-SJ90/33 GS-SJ25/25 | 350-500 | 400 |
GSPEG-630 | 315-630 | GS-SJ120/33 GS-SJ35/35 | 500-980 | 550 |
GSPEG-800 | 400-800 | GS-SJ150/33 GS-SJ35/35 | 800-1400 | 750 |
GSPEG-1200 | 800-1200 | GS-SJ150/33 GS-SJ35/35 | 800-1400 | 1200 |
High Output PE Extrusion Line Specification
Diameter(mm) | Host Model | Motor Power(KW) | Screw Rotation Speed(rpm) | Max. Output(KG/H) |
¢20-¢160 | G60/38D | 110 | 230 | 450-550 |
¢75-¢315 | G75/38D | 160 | 185 | 550-650 |
¢160-¢630 | G90/38D | 250 | 150 | 1000-1100 |
¢400–¢1200 | G120/38D | 315 | 106 | 1250-1400 |