PVC Pipe Extrusion Line
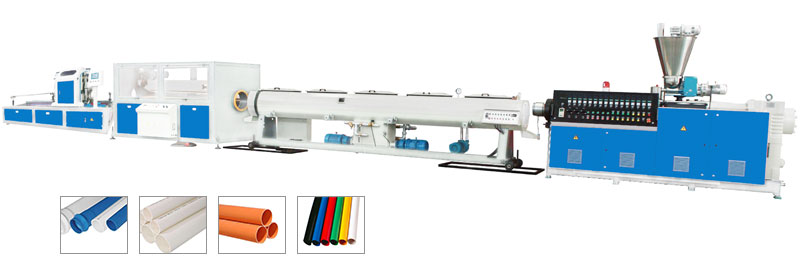
Pipe Diameter Range: Φ16 – Φ800
1. Mixing Raw Materials: PVC stabilizers, plasticizers, antioxidants, and other auxiliary materials are added to the high-speed mixer in proportion to the process, and the material is heated to the set process temperature by friction with the machine. The material is reduced to 40-50 degrees by cold mixer. Then it can be added to the hopper of the extruder.
2. Extruder Part: The machine is equipped with a quantitative feeding device to ensure stable extrusion. Due to the characteristics of the conical twin screw, the feed section has a larger diameter, which is beneficial to the plasticization of the material. When the screw rotates in the barrel, the PVC mixture is plasticized and pushed toward the head to achieve homogenization of compaction, melting, and mixing; and the purpose of exhausting and dehydrating is achieved. The feeding device and the screw driving device adopt frequency conversion speed regulation, which can realize synchronous speed regulation.
3. Extrusion Die Part: After compacting, melting, mixing and homogenizing PVC, the follow-up material is pushed to the die head through the screw, and the extrusion die is a built-up part of the pipe forming.
4. Vacuum Calibration Tank: It is used for shaping and cooling pipes with vacuum and water circulation systems installed. Also it is equipped with front & rear moving devices and left & right & height manual adjustment device.
5. Hauling-off Machine (frequency control): It is used to continuously and automatically pull the hardened pipe from the nose.
6. Cutting Machine: After the distance switch is controlled according to the required length, the automatic cutting is performed.
7. Stacker: The stacker turning is realized by pneumatic control through the air cylinder.
Layout:
Production Process Raw Material + Additive Preparation (Formula) → Mixing ( Mixer Unit) → Loading (Screw Loader) → Conical Twin-Screw Extruder → Extrusion Mould → Vacuum Calibration Tank → Crawler Hauling-off Machine → Lifting Cutter ( Planetary Cutter) → Stacker → Finished product testing packaging
Diameter(mm) | Φ50-160 | Φ63-200 | Φ160-315 | Φ315-630 | Over Φ630 |
Extruder Model | SJZ65/132 | SJZ65/132 | SJZ80/156 | SJZ92/188 | Customized |
Motor Power | AC 37Kw | AC 37Kw | AC 55Kw | DC 110Kw | Customized |
Capacity (Kg/h) | 180-250 | 180-250 | 300-400 | 400-800 | Customized |
Line Length (m) | 21 | 22 | 28 | 35 | Customized |